Experimental Lab
The experimental lab at Systems and Control is geared towards introducing students to hardware and software that implement control theories learnt as part of coursework. A variety of setups based on mechanical, electrical and chemical principles are made available to the students for this purpose. As part of core coursework all masters students are expected to understand modelling, communication, sensor calibration and control of hardware to accomplish different control objectives. In addition, several graduate students carry out a part of their research on these setups to validate control designs. As the group evolves and interests of the control community change, the specific setups that are part of the lab undergo upgradation or changes.
Following is the list of Facilities avalaible with us:
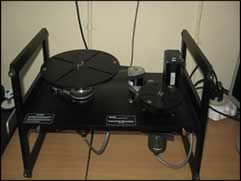
The Industrial Emulator is an electromechanical system that represents important classes of systems such as conveyors, machine tools, spindle drives, and automated assembly machines. The setup is provided by Educational Control Products (ECP), California, USA. The system consists of a drive disc which is driven through a drive motor (servo actuator). The drive disc is coupled to the drive motor through a timing belt. The motion of the drive disc is transferred to another disc in which a load disc is used to load the system. The motion from drive disc to load disc is transferred through a speed reduction assembly and a timing belt. The load and the drive disc inertia are adjustable. High resolution encoder is used to measure the position of load disc. The drive motor is driven by a servo amplifier. The system is tested for performance and robustness properties by different control algorithms like PID, Quantitative Feedback Theory and Sliding Mode Control.
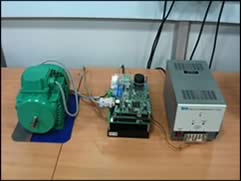
The Induction Motor setup consists of (a) Sieber make 3 phase, 230 Volts, 370 watts Induction Motor along with optical Encoder, (b) Technosoft make ACPM 750 Power Module., (c) Technosoft make MSK2812 DSP Board, (d) DMC Developer Pro IDE. The setup is used to explore various control strategies for IM control like Open & closed loop V/f Control, Direct & Indirect Vector Control, Sensorless control.
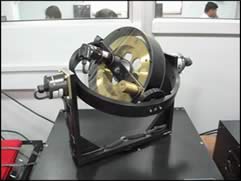
Any rotating body that exhibits two fundamental properties: gyroscopic inertia (rigidity in space) and precession (the tilting of the axis at right angles to any force tending to alter the plane of rotation). These properties are inherent in all rotating bodies, including the earth itself. The term gyroscope is commonly applied to spherical, wheel-shaped, or disk-shaped bodies that are universally mounted to be free to rotate in any direction; they are used to demonstrate these properties or to indicate movements in space. A gyroscope that is constrained from moving around one axis other than the axis of rotation is sometimes called a gyrostat. In nearly all its practical applications, the gyroscope is constrained or controlled this way, and the prefix gyro is customarily added to the name of the application, as, for instance, gyrocompass, gyrostabilizer, and gyropilot. Applications of the Gyroscope By using the characteristic of gyroscopic inertia and applying the force of gravity to cause precession, the gyroscope can function as a directional indicator or compass.
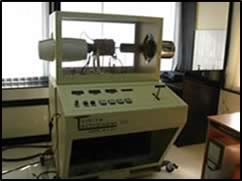
The Turbine Technologies Limited Minilab Gas Turbine Power System is a complete self contained jet engine lab which uses the SR30 Gas Turbine. It allows all aspects of the Gas Turbine theory to be easily demonstrated and explored. The SR30 is a pure turbojet and is representative of all straight jet engines in which combustion results in an expanding gas that is sufficiently capable of producing useful work and propulsive thrust. It consists of a centrifugal flow compressor, annular combustor and axial flow power turbine.

The unique MagLev apparatus from ECP demonstrates closed loop levitation of permanent and ferromagnetic elements. The apparatus includes laser feedback and high flux magnetics to affect large displacements and provide visually stimulating tracking and regulation demonstrations. The system is quickly set up in the open loop stable and unstable (repulsive and attractive fields) configurations shown. By adding a second magnet, two SIMO plants may be created, and by driving both actuators with both magnets, MIMO control is studied. The inherent magnetic field nonlinearities may be inverted via provided real time algorithms for linear control study or the full system dynamics may be examined. Disturbances may be introduced via the second drive coil for demonstrating system regulation in SISO and SIMO operation.
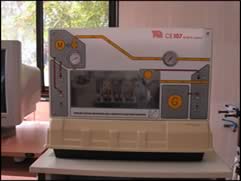
The Engine Speed Control setup (CE107) is a laboratory version of the standard engine control problem produced by TQ Education & Training Ltd., UK. It is the scaled model of a steam engine and is driven by the compressed air. Its main components are the air control valve (actuator) , the engine (four cylinders) and the load (flywheel as inertial load and electric generator as the variable load). One peculiar feature of the setup is the dead-zone nonlinearity present in the input characteristics of the valve. This makes the (otherwise simple) speed control objective quite challenging. The task can be further complicated by introducing a load disturbance.
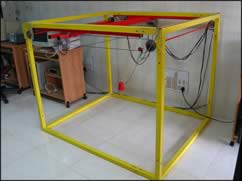
The 3D crane is a non linear electromechanical system having a complex dynamic behavior and creating challenging control problems. The system is controlled from a desktop computer. The setup consists of a payload hanging on a pendulum like lift line wound by a motor mounted on a cart. The payload is lifted and lowered in the Z direction while the rail and cart are capable of performing 2 DOF motion in horizontal plane. Hence, the payload can move freely in 3 dimensional space. The current research is focused at the point to point and trajectory tracking control while minimizing the payload swing.
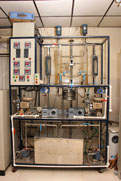
The hybrid two tanks setup is conceptualized, designed and developed by systems and control engineering group, IIT Bombay. It is developed to provide a common experimental platform for linear models, nonlinear models, SISO and MIMO systems, with or without delays, etc. The setup consists of two acrylic tubular tanks of similar dimensions with height of 60 cm and radius of 15 cm, a reservoir, two pumps, two heaters and a variety of valves and instrumentation in order to allow it to be configured in a variety of ways. Each tank has a heater, input flow line, stirrer with variable speed, separate drain valve to main drain. Tank1 and tank2 are connected to each other by means of valves. Valve 1 is a Packer valve which is used to define the interaction between the two tanks. The interaction between the two tanks can be quantified in terms of the number of exposed 93rings94. Valve 2 is also a Packer valve, but it is placed at a height of 30 cm from inlet to valve 1. This is to ensure that the plant model changes because of the interaction occurring at a defined time offset from the commencement of the experiment. The tank2 has a drain through the delay coil. The delay coil has two separate temperature sensors at two different points to provide two different delays in measurement. The quantitative feedback theory control algorithms have been successfully implemented on the setup.
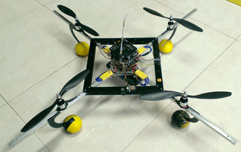
A quadcopter, also called a quadrotor helicopter is a multicopter that is lifted and propelled by four rotors. Unlike most helicopters, quadcopters use symmetrically pitched blades; these can be adjusted collectively. Control of vehicle motion is achieved by altering the pitch and/or rotation rate of one or more rotor discs, thereby changing its torque load and thrust/lift characteristics. These vehicles use an electronic control system and electronic sensors to stabilize the aircraft. With their small size and agile manoeuvrability, these quadcopters can be flown indoors as well as outdoors. The quadcopter is a complex flying machine but highly versatile with ability to perform many types of tasks. Quadcopters are symmetrical vehicles with four equally sized rotors at the end of four equal length rods. This system has been designed on the arducopter platform built on the ardupilot mega embedded board. All the four motors are controlled by independent ESC (Electronic Speed Controller) units, which generate a required RPM by applying a suitable PWM signal. The system hardware consists of several inbuilt sensors like GPS, IMU, SONAR, Xbee telemetry etc. which will facilitate autonomous flight. In the manual mode, the system is controlled by an 8-channel remote control (RC) while autonomous flight mode includes waypoint navigation, mission planning, loiter, autonomous takeoff and landing etc.
The experimental lab at Systems and Control is geared towards introducing students to hardware and software that implement control theories learnt as part of coursework. A variety of setups based on mechanical, electrical and chemical principles are made available to the students for this purpose. As part of core coursework all masters students are expected to understand modelling, communication, sensor calibration and control of hardware to accomplish different control objectives. In addition, several graduate students carry out a part of their research on these setups to validate control designs. As the group evolves and interests of the control community change, the specific setups that are part of the lab undergo upgradation or changes.
Following is the list of Facilities avalaible with us:
Industrial Plant Emulator
Induction Motor
Gyroscope
Magnetic Levitation
Gas Turbine
Engine Speed Control
3D Crane
Hybrid Two Tank Setup
Quadcopter
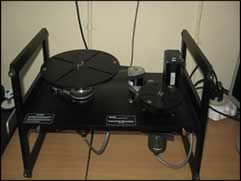
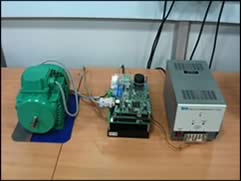
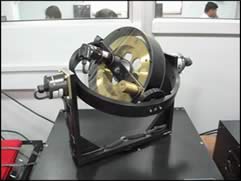
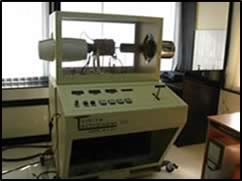

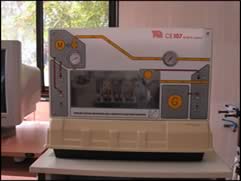
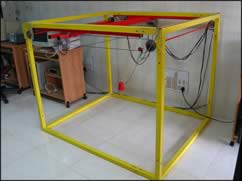
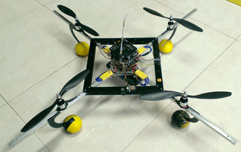
